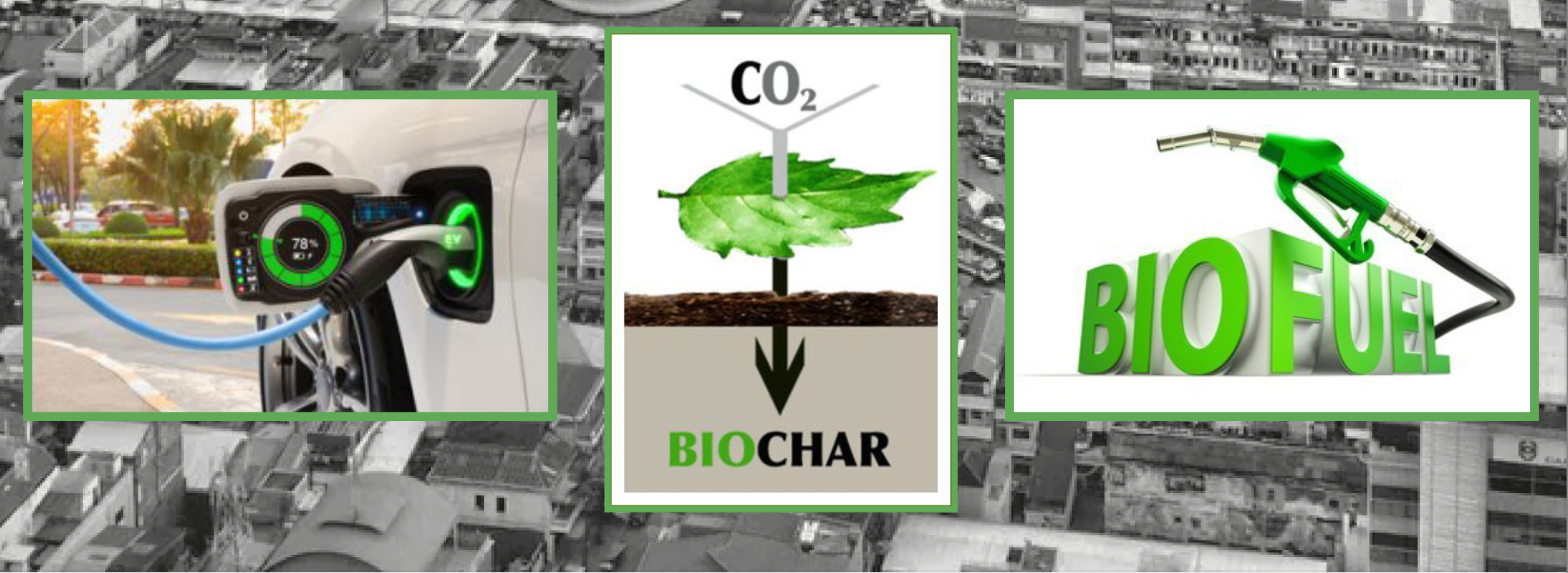
Global Green International Investments (GGII) Pyrolysis Technology
Advanced Pyrolysis is an endothermic reaction that results in the thermal decomposition of materials at high temperature in an inert atmosphere. As there is no oxygen present, the material does not combust but the chemical compounds that make up that feedstock material thermally decompose. In Pyrolysis processes, large and complex organic compounds are broken down into much simpler and smaller compounds. Some of these compounds evaporate and turn into gases, others turn into viscous, dark-coloured liquids, and cellulose and carbonation materials are generally converted to biochar and volatile compounds.
The main parameters governing the Pyrolysis process are temperature, heating rate, solid residence time, volatile residence time, particle size and density of particles. Pyrolysis is thus categorised into three major types: flash, fast and slow pyrolysis, based on temperature, heating rate, and residence rate. Hence the products of Pyrolysis vary dramatically in accordance to the type of Pyrolysis being used.

GGII Pyrolysis technology is proven leading-edge technology that our research has shown, surpasses all other Pyrolysis processes previously developed. It can safely and cleanly process a variety of waste products including ‘end of life’ plastics, biomass, refuse derived fuel, MSW, vehicle tyres, sewerage sludges, food and animal waste and medical waste. Unlike some incineration and gasification technologies that are designed to heat steam to create electricity and produce limited end products, GGII’s Pyrolysis Technology (Fast Pyrolysis) converts a wide variety of wastes into a range of products including:
- Syngas: used for power generation or cooled to produce Syn-diesel.
- Synthetic diesel: considered to be greenhouse gas neutral.
- Hydrogen: 99% pure via two stage reforming of syn-gas to hydrogen.
- Biochar: used to benefit soil quality and enhance crops.
- Activated carbon.
- Recycled steel from tyres (pre-sorted prior to the Pyrolysis process).
- Carbon credits to be sold to the Global carbon credit market.
GGII Pyrolysis technology uses superheated steam in the later stage of the Pyrolysis treatment process to further increase the quantity of hydrocarbons which enrich the heating values of Pyrolysis oil compared to traditional Pyrolysis treatment processes, having lower heating values. GGII overcomes the low heating and calorific values of Pyrolysis oil by refining the synfuel to EN590 grade diesel, using an advanced oil refinery technology after Pyrolysis oil has condensed and cooled. This treatment process follows the post Pyrolysis oxidization of the melt to produce the syngas and hydrocarbon condensates having much higher heat values from 15 to 20 MJ/Nm3.

GGII Pyrolysis technology is superior to comparative Pyrolysis, incineration and gasification technologies due to the following features:
- Provides an integrated total recycling solution as part of the Circular Economy, producing valuable products from waste that traditionally cannot or is not recycled.
- Reduces waste to landfill with lower waste disposal landfill development costs and new landfill acquisition costs.
- Uses proven technology with plants in Korea in operation since 2002.
- Works with specialised tech partners from Hitachi, Mitsubishi and Tipton Ceram.
- Employs a modular design which can be easily scaled up to meet increasing waste quantities.
- Uses flexible waste feedstock (MSW, agricultural residue, biomass industrial waste, tyres, plastic and rubber, medical wastes, and sewerage sludge.
- Produces high calorific value refined fuels and industrial oils.
- The syngas produced fuels electric turbines and is capable of being carbonised to graphene and production of hydrogen fuel cells.
- The patented Pyrolysis technology has a high energy efficiency including 34% for diesel configurations, 50% -60% for hybrid fuel and all electricity plant configurations.
- The facilities are self-sufficient for in-house energy consumption for the entire production process.
- The facilities produce “continuous power”.
- Plant emissions meet or exceed global air, soil and groundwater emission standards including in US, Australia, Canada, Europe, South Korea and Japan.
- Produces very low amounts of CO2, SoX, NOx, CH4 and dioxin.
- Reduces greenhouse gases and has very low air and leachate emissions.
- Replaces and reduces the dependency of fossil fuels through the production of electricity, EN590 grade diesel, oil & lubricants and biochar.
- Has financial attractive returns for investors, equity partners and stakeholders.