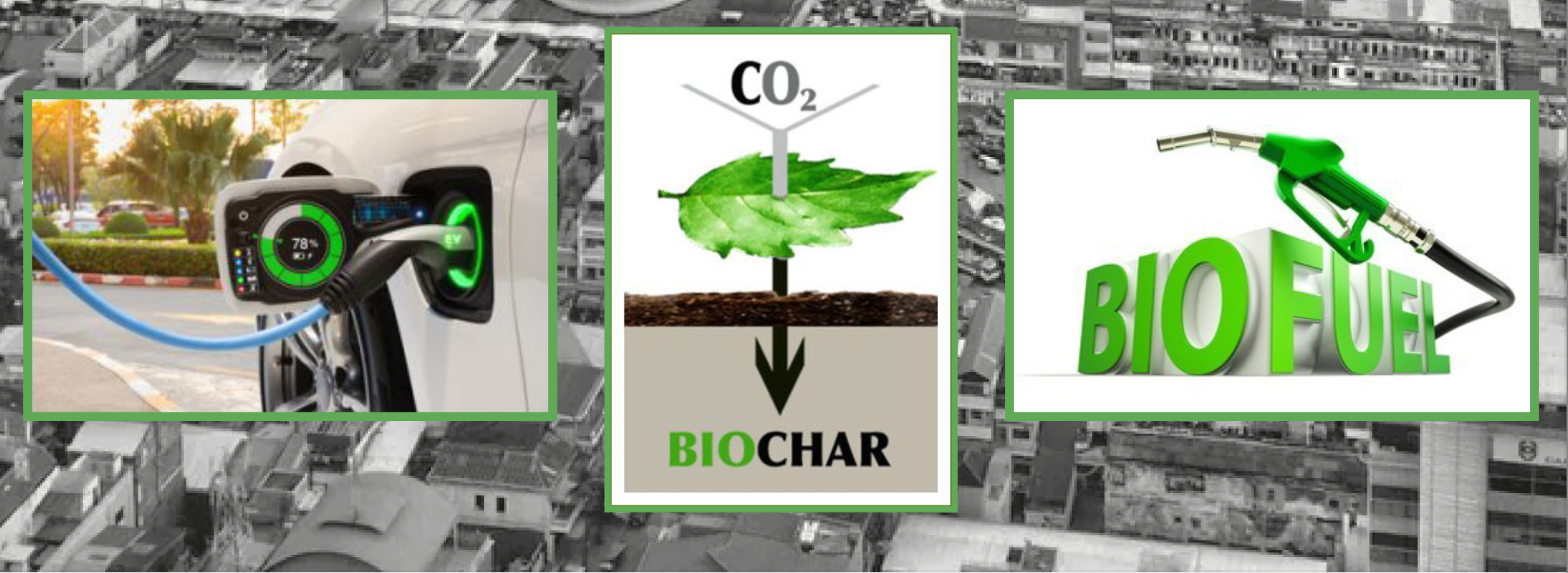
Our Renewable Products
Electricity
Hybrid and all-electric plants convert syngas and heat to electricity through the use of turbines or Rankine heat generators. 85% of the waste heat collected can be used to generate electricity using a Rankine Cycle system that is 36% efficient (overall electrical efficiency is 30.6%). heat is also important to maintain the system’s internal environment and components at optimum temperatures through conduction. GGII Pyrolysis guarantees that a single all-electric plant line will generate 77,995 kWh (3.6 MWh continuous) and hybrid plant line 38,997 kWh (1.8 MWh continuous). Actual production outputs are typically 15% higher depending on the calorific value of feedstocks.
Hydrogen Fuels
Syngas produced through the Pyrolysis process is capable of being carbonised to graphene and the production of hydrogen fuel cells. Pyrolysis syngas is re-formed via two-stage processes into hydrogen, up to 99.9% pure. The hydrogen may be stored in bulk, or adapted for fuel cell technology, and outputs are expected to be around 800,000 kg’s per annum per plant line. While renewable electricity is destined to power the international small transportation needs, hydrogens superior energy performance will power heavy industry including international air and shipping, and heavy haulage vehicles. GEI Mekong seeks to enter new markets for its waste-to-energy facilities for impending changes in the fuel market, by looking to convert the syngas via carbonisation, to carbon nanotubes for batteries and hydrogen fuel cells for motor vehicles. The syngas contains ~37% Hydrogen.
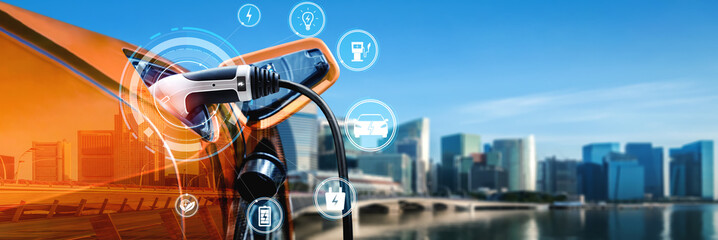
Synfuel
There are minimum and maximum values which the fuel must meet in order to be classed as EN590 grade diesel or oil. The typical column lists values for these parameters, all of which lie within the specification limits and which can be expected for deliveries of this grade fuel. These parameters include density at 15 degrees Celsius (typically at this temperature it will have a density of ).856kg/m3 with a minimum of 0.82kg/m3, a typical 0.1% carbon residue value (where the maximum permitted for this grade os 0.3%). The minimum flashpoint (the lowest temperature at which the fuel produces vapour that is an ignitable mixture in air near the surface of the liquid) is 56 degrees Celsius, while typically you can expect A2 Class gas oil to have a flashpoint of more than 62 degrees Celsius.
Other important parameters that this grade of oil needs to meet are the cold filter plugging point in winter and summer (the highest temperature at which point the oil will start to gel and cause filter blocking issues). Class A2 gas oil needs to stay fully mobile down to a maximum of -4 degrees Celsius (the typical plugging point is -8 degrees Celsius in summer0 and -12 degrees Celsius in winter (typically A2 gas oil maintains full fluidity until -15 degrees Celsius. GGI Pyrolysis guarantees that single synfuel and hybrid plant lines will produce a minimum of 11.200 litres of EN590 grade diesel. With high calorific feedstocks, production levels typically exceed 14,000 litres of EN590 grade diesel.
Oils and Lubricants
Synthetic pyrolytic derived oils and lubricants from the Pyrolysis process include, Heavy bunker oil, Heating oil, Hydraulic oils, Greases, Gear oil, Transformer oil, Metal working and industrial cutting oils, Process oils for industry. GGII Pyrolysis guarantees that single synfuel and hybrid plant lines will produce a minimum of 2,800 litres and 3,000 litres of synthetic oils respectively.
Biochar
GGII Pyrolysis plants create Biochar, a significant co-product of the Pyrolysis process that has properties similar to coal. At 23-32 GJ per ton, pyrolysis Biochar has a higher heating value than many grades of coal and it is also green fuel that is CO2-neutral. Biochar can be used as a substitute for other industrial fuels to produce the heat required for drying the feedstock and/or to supply heat to the Pyrolysis reactor. In pelletised form it can feed the boiler to generate further energy for electricity production.
The addition of Biochar to agricultural soils is receiving much attention due to the benefits to soil quality and enhanced crop yields and the potential to gain carbon credits by active carbon sequestration. Studies have shown that Biochar can significantly contribute to: decreasing soil acidity, nutrient retention and caption exchange capacity, decreased uptake of soil toxins, improving soil structure, nutrient use efficiency, water-holding capacity, decreased release of non-CO2 greenhouse gases, a high and long term ability to absorb (sequent) carbon dioxide produced by pyrolysis processes, achievement of Korean toxicity standards for heavy metals, persistent organic compounds, and benzines.
Importantly, Biochar reduces greenhouse gas emissions by sequestering carbon in inert charcoal that decomposes more slowly than the original feedstock used to make the charcoal. Recent study estimates report that one metric ton of Biochar sequesters between 1.7 to 2.35 metric tons of carbon dioxide.
Carbon Black
The Pyrolysis process will deliver 20% to 30% char which can be further refined and turned into a carbon black which is used as a feedstock for the production of new tyres. Commercial Carbon Black (CB) is a rich-carbon material widely used as reinforcing filler in rubber goods. When waste tyres are transformed by Pyrolysis, the obtained solid fraction known as pyrolytic carbon black (CBp) contains the original CB (80-90 wt.%) and is added in tyre manufacturing process along with sulphur (1-3 wt). Carbon Black has the ability to conduct heat away from the tread and belts of the tyres, which helps to increase the lifespan of the tyre. Carbon Black compounds also help protect the tyres from UV rays and ozone, which would otherwise shorten their lifespan.
Carbon Credits
GGII Pyrolysis line emissions will equal to 88 metric tonnes of carbon credits per day; equal to 30,800 metric tonnes per year. The importance to the waste management sector with respect to carbon abatement is the capture and the methane which has 80 times the heating potential of CO2; making pyrolysis and bio digestion technologies the leaders in reducing methanation from landfills.
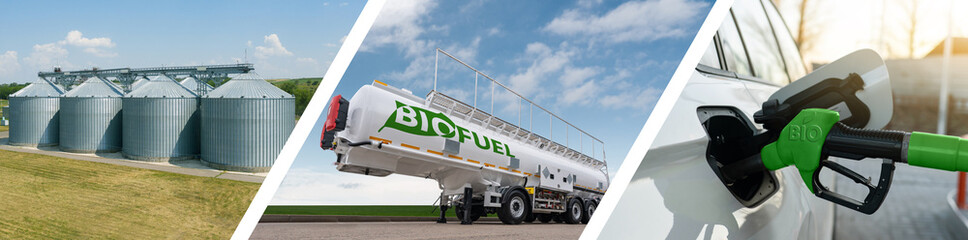