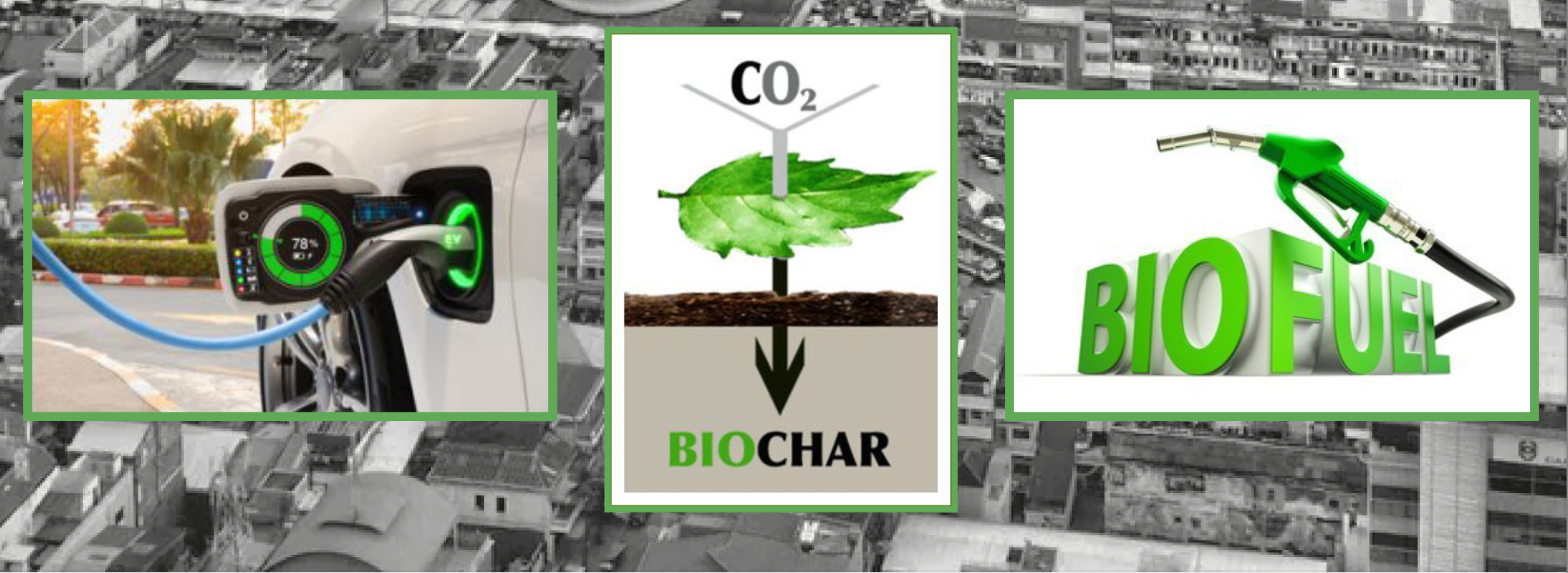
Environmental Safeguards
As part of GEI Mekong’s commitment to ESCG, the company adheres to international environmental safeguards implemented as international treaties, government laws, policies and regulations, as well as those used by multilateral development banks including the Asian Development Bank (AND), World Bank (WB) and the African Development Bank. GEI Mekong observes international treaties including the Convention on the Prevention of Dumping of Wastes and other Matter (London Convention), which is an international treaty that limits the discharge of wastes generated on land and disposed of at sea (1972). The Basel Convention regulates the transboundary movements of hazardous wastes and other wastes and obliges its Parties to ensure that such wastes are managed and disposed of in an environmentally sound manner.
GEI Mekong will complete the necessary environmental assessments to acquire the statutory environmental licenses top operate its facilities. The Initial Environmental Examination (IEE) will include a site-specific Environmental Management Plan (EMP) which covers the pre-construction, construction and post construction periods.
The IEE will address:
- the management and monitoring of air emissions.
- waste water and effluent management.
- noise and odour control and abatement.
- storm water management.
- vector and dust control.
- fire controls.
- residual containment of MSW.
- weigh bridge and traffic management controls.
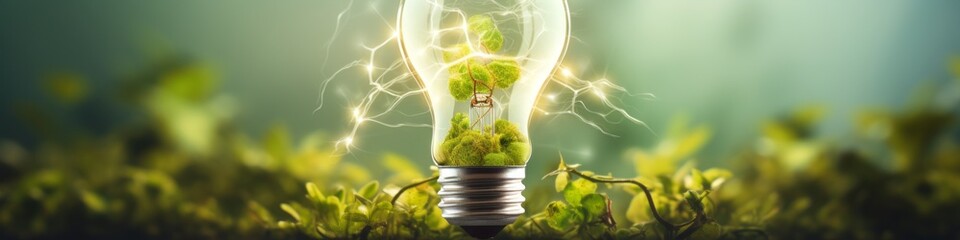
The quality of air and water discharged from the facility will be measured and monitored on a daily and weekly basis (air stack emission will be monitored in real time). Surrounding soil, air, and ground water will be monitored monthly and quarterly. Monthly and annual environmental performance reports will be submitted to regulatory bodies and will include accurate waste accounting of MSW delivered by waste collection companies, recyclables and inert materials.
Treatment and In-plant Recycling of Waste Water
GEI Mekong’s facilities will not discharge waste water or leachate to adjacent land or waterways. Process water will either be discharged to the atmosphere as waste steam or collected and sent to the onsite Anaerobic Baffle Reactor Compact Wastewater treatment plant (ABRC) for treatment and reuse within the facility. The short term municipal solid waste (MSW) storage area will be established in a fully sealed and bundled holding area under a negative vacuum at the front end of the materials recovery facility (MRF). Leachate from the short term area and MRF (pre-treatment facility), will flow via gravity ti inceptor surface drains and underground leachate collection piping to a 30,000 litre collection tank, which forms the first stage of the ABRC.
The second stage of the ABRC will comprise covered settlement tanks with a capacity of 80,000 litres where leachate is given 3 days to solidify and settle suspended solids. Sediment will be removed from the settlement tanks on scheduled periodic basis, dried and mixed with sorted MSW as dry cake and used as feedstock to produce RDF. The wastewater is then pumped into the ABRC reactor clarifier tanks and is chemically treated so that the water can be reused in the facility. The reclaimed water is stored in a 10,000 litre tank for cooling, converted to steam to drive various system components, with excess water released to the environment via the flu stack emissions system.
Fuel Storage
Fuel storage will meet and exceed the relevant government requirements. International and national distribution will be outsourced to a licenced distributor that have acquired international ISO certifications 9001 (management quality), 14001 (environment) and 45001 (occupational health and safety).
Diesel, oils and lubricants will be stored in above ground silo tanks in an area close to the backend oil refinery. The silos will have capacity for up to 200,000 litres and be de-cantered into 28,000 litre ISO containers in a fully bunded concrete area. The ISO containers will be fork crane lifted onto semi-trailers, secured and transported offsite. There will be no discharges of fuels and oils to areas outside the bunded containment area. Emergency SOP’s for accidental spillage will form part of the facilities emergency response regime.
Air and Flue Gas Stack Emissions
Extensive testing has been performed on GGII’s systems and facilities over many years of operation. Continuous efforts through R&D have resulted in the reduction of GHG with the net quantity of flu gases being minimised. The results of independent testing indicates that the exhaust gases from GGII’s pyrolysis plants contain little or no toxic substances or GHG emissions, and fully comply with international air emission standards. Furthermore, it is evident that the emissions do not contain greenhouse gases.
Odour
The highest ground level concentration of odour is targeted at 99.9 odour Units (Ou). The OU level is low and will not be detectable to the existing background OU levels. The facility is equipped with odour abatement filters and a negative vacuum exists within the main pyrolysis building which will ensure that odour is contained within the main building.
Dust Control
Dust and airbourne particulates that are produced by vehicles outside the pyrolysis building will be controlled through regular cleaning of internal concrete roads and paved areas. The facility’s truck washing station will further reduce the generation of dust from incoming waste collection vehicles. All mobile plant and stationary equipment operating outside the main pyrolysis building will be new and fitted with the manufacturers emission compliant exhaust systems which will be maintained at the facilities onsite workshop.
Noise
Based on environmental impact studies already completed, GEI Mekong’s facility will comply with the relevant government noise attenuation standards. These noise abatement standards will be validated during the environmental assessment and permitting phase under the relevant EPC contracts. Equipment rated to emit significant levels of noise along with respective hours of operation is calculated with reference to the installed plant and machinery inside and outside the main facility building.
Materials handling and processing equipment includes mobile machinery, shredders and trommels, hoppers and crushers, conveyor systems and electric turbines (for electric and hybrid configurations). These range from 28 to 56 dB(A). The estimation for noise sources at the point immediately outside the building’s external walls indicate that a noise from these sources will be “inaudible at the nearest sensitive receptors” and sound power level of emission from each source is less than 80db(A).